What are the commonly used welding methods for oil pipelines
TICO introduces some commonly used pipeline processing techniques, mainly including Manual Arc Welding, TIG Welding and Automatic Welding, which enhances your confidence in our products.
Manual Arc Welding
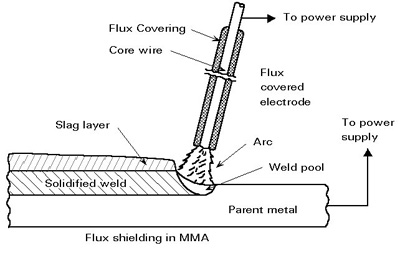
Manual arc welding is a method of arc welding by hand welding electrode. The thickness of the weldment by manual arc welding is above 1.5mm . Therefore, it is suitable for welding of carbon steel, low alloy steel, stainless steel, heat-resistant steel, low temperature steel, copper and copper alloy material, cast iron welding and surfacing of various materials. Manual arc welding has the following advantages.
- Flexible technology: Suitable for all kinds of structures, shapes, welding in various positions and the accuracy of the welding joint device is not high.
- High adaptability: It is suitable for welding many metal materials of different thickness.
- It is easy to control the deformation of workpiece by process adjustment, which can improve stress state.
- The equipment is simple and it’s easy to operate and maintain that welding can be carried out within the plant and in different construction operations.
Of course, manual arc welding is also inadequate. Its production efficiency is low, labor intensity is great, and the welder's operation technology requirements are higher.
Gas Tungsten Arc Welding
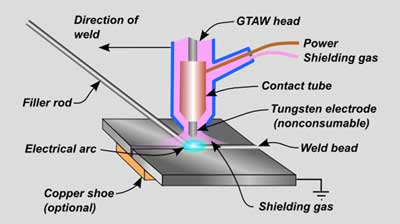
Gas tungsten arc welding is often referred to as TIG welding. It is an arc welding method that produces heat between non expendable electrodes and work piece. Electrodes, rods, bath, arc, and work near the heating area shall be isolated from the atmosphere. This protection is supplied by a gas or mixed gas stream and must be able to provide full protection, because even a tiny amount of air will contaminate the weld. A constant-current welding power supply produces electrical energy, which is conducted across the arc through a column of highly ionized gas and metal vapors known as a plasma.
GTAW is most commonly used to weld thin sections of stainless steel and non-ferrous metals such as aluminum, magnesium, and copper alloys. GTAW is very stable and can be stably burnt even under very small current. Therefore, it is especially suitable for welding thin plate material. The heat source and the filler wire can be controlled separately, so the heat input is easy to adjust, so the welding method can be welded in all directions, and is also an ideal method for realizing double sided welding of one side welding. The process grants the operator greater control over the weld than competing processes such as shielded metal arc welding and gas metal arc welding, allowing for stronger, higher quality welds. However, GTAW is comparatively more complex and difficult to master, and furthermore, it is significantly slower than most other welding techniques. A related process, plasma arc welding, uses a slightly different welding torch to create a more focused welding arc and as a result is often automated.
Automatic Welding
Semi automatic welding usually refers to the feeding of the welding wire by automatic delivery, but the welding torch moves along the weld line and moves by hand. Such as MIG is semi-automatic welding. Fully automatic welding is the technical measure of automatic operation, according to prescribed procedures or instructions, whose purpose is to increase production, improve quality, reduce costs and labor intensity, and ensure production safety.
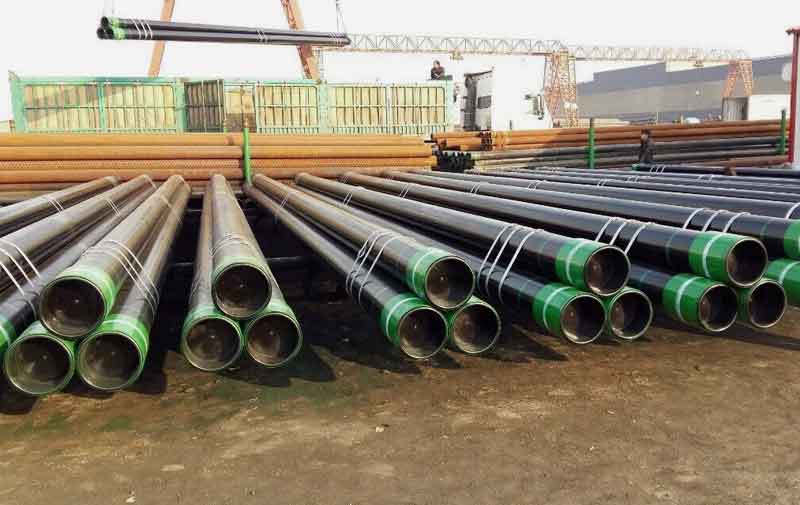
The degree of automation has become one of the important symbols to measure the level of modern national science, technology and economic development. Modern automation technology mainly relies on computer control technology to achieve. Welding automation is the development direction of welding structure production technology. In the welding equipment, apply microcomputer automatic control technology, such as CNC welding power supply, intelligent welding machine, automatic welding machine and flexible welding robot workstation. The function of microcomputer control system in all kinds of automatic welding and cutting equipment is not only to control all welding parameters, but also must be able to automatically coordinate the whole set of welding equipment parts of the operation.