Some inspection processes about welded pipeline
Basic requirements for pressure welded pipe appearance
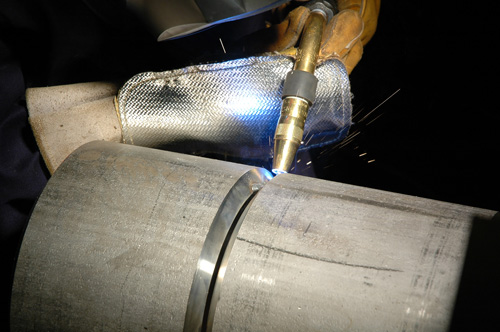
The appearance of the welds shall be in accordance with the requirements before non destructive tested of welded pipes. It is generally required that the appearance of the welded joint of the pressure pipeline is in a neat shape, and the welded joint is of good quality. The width of each side welded joint is 2mm. The welding leg length of fillet weld should meet the design requirements, and the level of regulation of small form factor should be smooth transition.
Cracks, lack of fusion, porosity, slag, spatter exist is not allowed in the surface of welded joint.
The design temperature of pipeline is lower than -29 degrees, fan ruler of hardened stainless steel and alloy steel pipes tend to be larger weld surface, without undercut. The undercut of pipe weld should be greater than the depth of 0.5mm, the continuous bite undercut should not be greater than 100mm, and both sides of the weld undercut grow at 10 percent of the total weld length. The surface of the welded seam is not less than that of the pipe. The thickness of the weld reinforcement is not more than 3mm. The wrong side wall thickness of welded joints should not exceed 10% and not more than 2mm.
On the surface of nondestructive testing
The principle of nondestructive testing method for surface pressure pipeline: The magnetic iron used in magnetic particle inspection; Non-ferromagnetic steel should be used in penetration testing. There is a tendency to delayed cracking of welded joints, the surface should be non-destructive testing of cooling after welding certain time; reheat cracking tendency of welded joints, the surface should be in non-destructive testing and post-weld heat treatment once each.
Ray inspection & ultrasonic testing
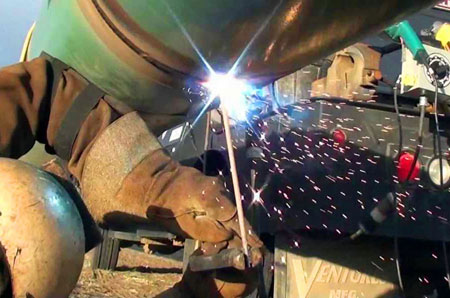
Ray inspection & ultrasonic testing is common inspections of pressure piping and pipe joints. Titanium, aluminum and aluminum alloy, copper and copper alloys, welded joints to detect nickel and nickel alloys, and should be used in radiation detection methods. There is a tendency to delay weld cracks, its ray inspection and ultrasonic testing should be at a certain time of cooling after welding.
The weld should be operating 100% ray detection when the head of a folder inside the casing has a girth weld. Covert operations can be carried out after passing through the pressure test. Reinforcement rings or bearing plate covered with welded joints should be carried with 100% of the pipe-ray inspection and covered after passing. Inspection in the provisions of the welding, non destructive testing should be carried out after visual inspection. Radiography and ultrasonic testing shall be carried out, and the surface of the non-destructive testing shall be carried out after the test welds shall continue to be evaluated.