Do you know new anti-corrosion technologies for pipelines
Water injection technology and hydrochloric acid cracking are often used to increase the concentration of Cl ion in oil and gas. At present, the main material used in drilling, gathering and transporting equipment in oil and gas fields is steel, while the corrosion resistance of iron and steel materials against H2S and Cl ions is poor, that results in corrosion of pipes and equipment exposed to H2S and Cl media. Two new types of pipeline corrosion protection technology are introduced by TICO.
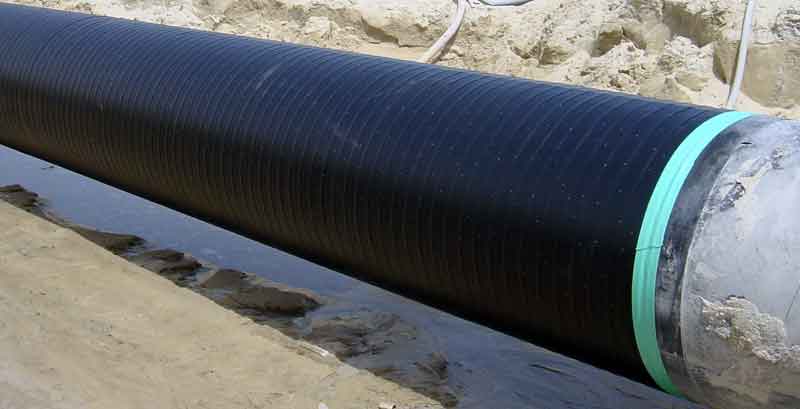
Add imidazoline inhibitor to prevent corrosion
In view of the corrosion caused by H2S, it is one of the most practical methods to protect pipeline and equipment by adding corrosion inhibitors. Corrosion inhibitors can be divided into organic corrosion inhibitors and inorganic inhibitors. Scholars at home and abroad have studied the mechanism of organic inhibitors and have mastered the process of chemical reaction between organic inhibitors and metal surface.
Imidazoline derivatives have the advantages of low toxicity, harmlessness, high efficiency in organic release agent. It can adsorb the metal surface with its own chemical adsorption, thus effectively inhibiting the uniform corrosion of the metal equipment under acidic conditions.
Corrosion rate of equipment after adding Imidazoline Inhibitor
Temperature(℃) | Additive Concentration(mol/L-1) | Buffer Concentration(%) | Protection Efficiency(%) | Corrosion Rate(mm/a-1) |
---|---|---|---|---|
56 | 0 | 0 | 0 | 2.2573 |
1.07×10-3 | 0.06 | 81.9 | 0.4024 | |
2.15×10-3 | 0.11 | 92.06 | 0.2732 | |
4.42×10-3 | 0.21 | 94.09 | 0.2339 | |
5.5×10-3 | 0.26 | 95.02 | 0.2115 | |
6.58×10-3 | 0.31 | 98.75 | 0.0301 | |
8.54×10-3 | 0.41 | 99.50 | 0.0126 |
As can be seen from the chart, the corrosion rate of N80 steel decreased obviously, and the corrosion rate of N80 steel decreased with the increase of concentration of imidazoline inhibitor. When the amount of corrosion inhibitor is 8.54 * 10-3mol/L, the corrosion rate of pipeline steel for oil well is reduced from 2.2573mm/a to 0.0126mm/a, and the corrosion rate of N80 steel is reduced by about 180 times. At this time, the steel has basically become a corrosion resistant material.
When the inhibitor was added and reached a certain saturation concentration, the corrosion rate of steel decreased more slowly than it began at the beginning. The reason for this is that if the inhibitor concentration increases continuously, the amount of adsorption on the surface of the sample will increase and the corrosion rate will decrease. If the corrosion inhibitor has exceeded the accurate dosage, the corrosion inhibitor will not change too much on the surface of steel, so the situation that the amount of inhibitor increases and the corrosion rate changes little occurs.
QPQ anticorrosion technology
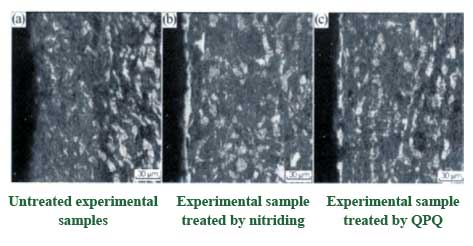
The essence of QPQ (Quench-Polish-Quench) technology is low temperature salt bath nitriding + salt bath oxidation or low temperature salt bath nitrocarburizing + salt bath oxidation. It has the advantages of high wear resistance, high corrosion resistance, micro distortion and so on. It is a new surface modification technology for metal parts. The surface of the equipment treated by QPQ is an oxide film of Fe3O4, and its corrosion resistance is much higher than that of nickel plating and chrome plating. Moreover, QPQ technology can also be used instead of phosphating and blackening and nickel plating to compare the traditional anti-corrosion process. The following experiments are conducted to investigate the corrosion resistance of N80 steel for oil well tubes after the use of QPQ Technology.
From the experimental results, it can be seen that the corrosion rate of the nitrided sample is 57% of the corrosion rate of the untreated experimental sample. The corrosion rate of samples treated by QPQ technique is 32% of the corrosion rate of untreated experimental samples and is 58% of the corrosion rate of the treated samples. So it can be proved that the experimental sample QPQ processing technology in the specific case of the corrosion resistance is the best, the pipeline equipment QPQ technology processing can be a long time placed in the air, and will not rust, do not change color.
In the production of oil and gas fields, many oil pipelines have already undergone chemical reactions before they go down, and become rusty. The petroleum pipeline treated by QPQ technology has been exposed to the air for a period of time before the downhole operation, and its corrosion resistance is much higher than that of the nitrided and raw raw materials. Using QPQ Technology is best choice to reduce the corrosion rate of the oil and gas pipelines before you go down the well. For the oxygen bearing corrosive media under the ground, the corrosion resistance of the sample treated by QPQ technology will be much higher than that of untreated and nitrided samples.
Conclusion
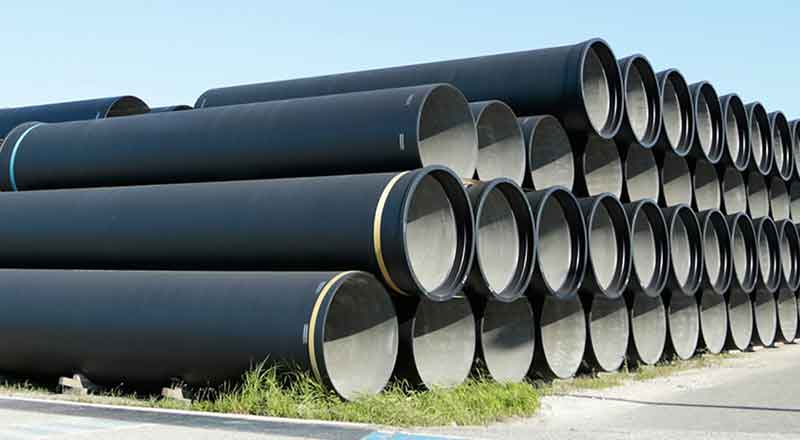
The corrosion prevention of petroleum pipeline has become a special concern of petrochemical enterprises. How to maximize the benefit by using the best technology has been the focus of research. TICO company come to conclusion according to experiments: Adding corrosion inhibitors and using QPQ technology has certain application value for pipeline corrosion protection.